The Little Bracket That Could!
Via initial introduction by Altair’s Ernst Burger, the Eco-Car Project has partnered with U Stellenbosch’s CT Scanning Centre and their research into both metal 3D printing and lattice structure design integrity conducted by Prof Anton du Plessis, the Managing Scientist at the Facility.
This partnership arose from the CT Scanning Centre’s CPAM funding and was initiated on the basis of producing working & load-bearing components in Ti-6-4 via metal 3D Additive Manufacturing, which could then be tested for integrity, as well as deployed on a working application.
This all part of a national research effort into establishing standardization of MicroCT non-destructive testing/analysis techniques to improve the accessibility and cost effectiveness of the 3D metal AM process in order to promote wider uptake of the process to users in the Additive Manufacturing community, and thereby, not only establish recognized standards and data output, which currently do not exist other than a few generic standards for scan parameters and best-practice methods, but to also establish South Africa as a leading proponent of metal AM, particularly aligning with the country’s rich titanium reserves.
A component on the NMU Eco-Car was identified as being an ideal initial project to satisfy these requirements - the mount for the front corner of the Eco-Car existed as a carbon-fibre bracket (see below) and had been in operation for two full competitions already. The objective here was to create an ultra-lightweight topology optimized version that could be printed in Titanium Ti-6-4 at multiple centres and then tested via microCT to see whether significant differences occurred in the printing processes iro porosity, flaws and geometry deviation. These would also then be compared to results from a 10 mm cube coupon which would undergo exactly the same tests.
In the few months this partnership has been active, the relationship has gone from strength-to-strength, and a topology optimized front corner bracket (C-Bracket) initially had been printed in Ti-6-4 at several centres in a round-robin experiment, including a NASA facility in the US.
Several of the initial prints were delivered to the Eco-Car lab and fitted onto the Eco Car, and the rest underwent material integrity testing at the CT Scanning Centre, with the best outputs being installed on the Eco-Car for the 2018 Shell Eco-Marathon competition. The Eco-Car went on to become three-time Champions in the event with the C-Bracket still to this day being installed on the vehicle and performing flawlessly.
All the design work was carried out utilizing Altair’s suite of products, specifically Altair Inspire’s cutting-edge topology optimization and lattice design capability.
The Eco-Car design team has also had the functionality of utilizing the CT Scanning Centre’s high-spec workstation remotely to help speed up the iterative analysis process, which is extremely computationally demanding.
This little bracket would go on to feature in many papers, presentations, articles and expos across the globe in the following months and years, several of which are displayed below. As such it was the starting point of the AEDG's design for additive manufacturing programme and continues to show its influence...
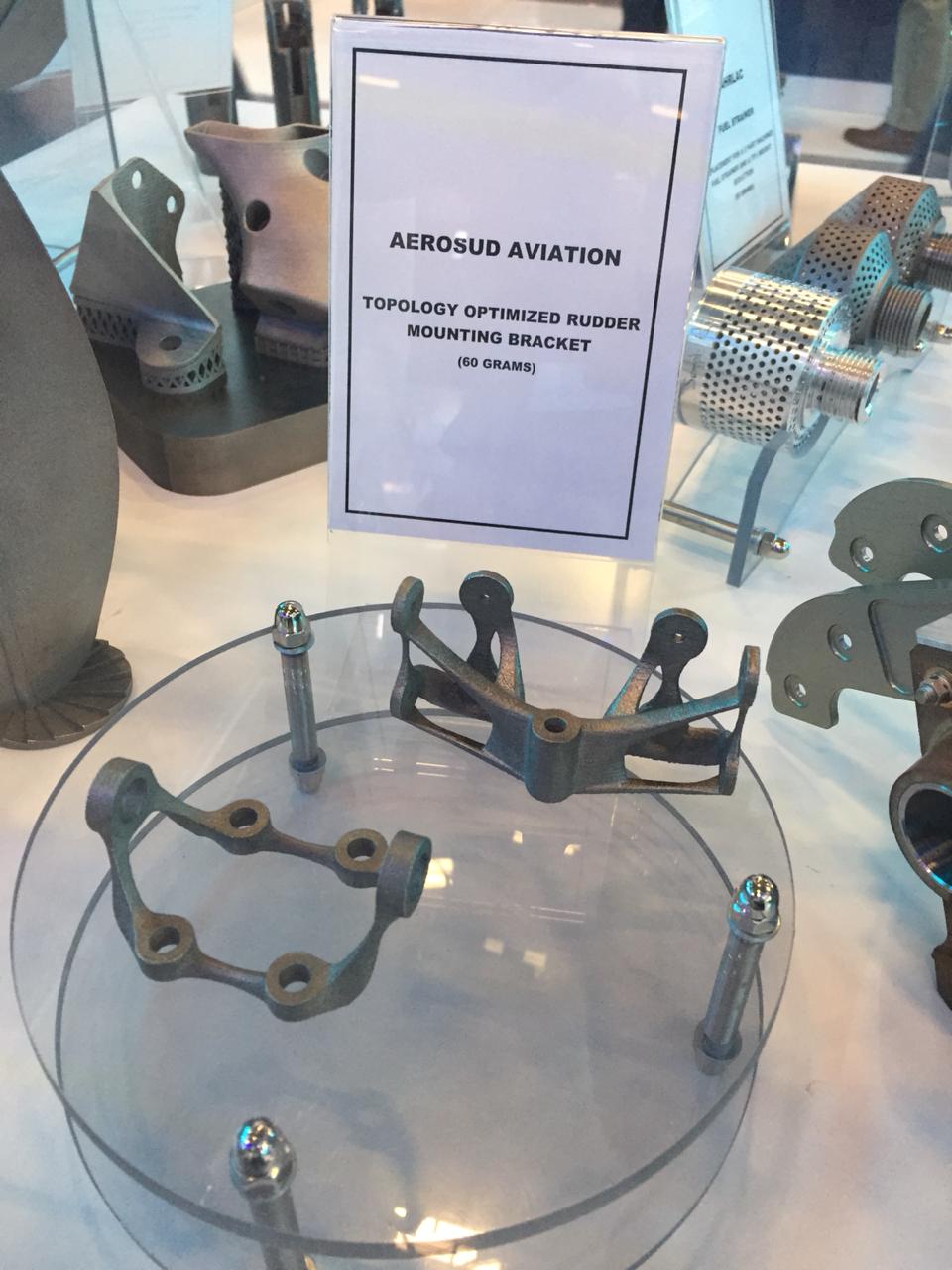
Research Papers
X-Ray Mico-CT Supporting the South African Additive Manufacturing Community A. du Plessis and S.G. le Roux
Can Additive Manufacturing Help Win the Race? CH Hands, A Du Plessis, N Minnaar, BA Blakey-Milner and EH Burger
Beautiful and Functional: A Review of Biomimicry in Additive Manufacturing Anton du Plessis, Chris Broeckhoven, Ina Yadroitsava, Igor Yadroitsev, Clive H. Hands, Dhruv Bathe
Webinars
ASME Webinar: Extreme Lightweighting Applications using Lattice and Topology Optimization in Inspire CH Hands, N Minnaar, BA Blakey-Milner